
Large Scale Metal Scavenging and Associated Decolorization at CARBOGEN AMCIS Shanghai
DIARIES OF A DRUG MANUFACTURER IN CHINA
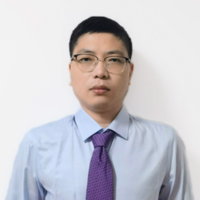
By Jun Tang, Ph.D.
Head of Development, CARBOGEN AMCIS Shanghai
Why is metal scavenging critical in pharmaceutical manufacturing?
Transition metal catalyzed carbon-carbon and carbon-nitrogen bond forming reactions, such as the Buchwald-Hartwig reaction, the Heck reactions and the Suzuki type reactions, etc. are widely used in small molecule synthesis in the pharmaceutical industry. A common problem of these reactions is high metal content in the product due to inefficient removal of metal residue as they are mostly homogeneous catalysts. On the other hand, heavy metal residue usually results in unexpected color of pharmaceutical intermediates or even APIs. Therefore metal scavenging and decolorization are critical in pharmaceutical manufacturing.
Pharmaceutical Guideline and regulations
ICH Q3D[1] presents a guideline for the assessment and control of elemental impurities in drug product. The control of heavy metal in drug product is crucial since any metal present is passed on to drug substance according to the dosage forms – this poses a high requirement on minimizing the residual metal content in drug substance.
In addition, the European Medicines Agency Committee for Medicinal Products for Human Use had given a guideline (now superseded by ICH Q3D) on control of residual metal catalysts and reagents[2].
What technologies are commonly used in pharmaceutical industry for metal/color removal?
In some cases removal of metal/color can be simply achieved by washing/extraction, precipitation and crystallization. But often the above techniques are incapable to reach regulatory acceptable (ppm) levels. The use of functionalized silica as metal scavengers, or charcoals, are becoming increasingly common in the pharmaceutical industry.
What are main challenges of metal scavenging and decolorization for pharmaceutical manufacturers?
First, the product bearing heteroatoms and electron-rich functional groups could bind to the metal scavenger or charcoal, incurring significant loss, therefore it is essential to screen the right scavenger and conditions to minimize losses. Unfortunately, it is not easy to simulate a production setup for scavenging process in lab scale.
Second, the cleaning of the reactor is extremely challenging if charging the metal scavenger or charcoal directly into the reactor.
Third, in-process control of the scavenging process to determine an appropriate end point can be a challenge because ICP-OES is not always available. In addition, preparation of an acid solution after ignition, ashing and digestion is not practical as an in process control.
Pharmaceutical manufacturers in China: what are the solutions from CARBOGEN AMCIS?
In-line scavenging that puts scavengers/charcoal into cartridges is a perfect solution.
The CARBOGEN AMCIS Shanghai R&D team has extensive experience with the screening of metal scavengers and process development of the in-line scavenging technique. The in-line circulation of product solution is realized by peristaltic pump (Figure 1) while the cartridges are exchangeable in pressure housings (Figure 2). This is a close simulation of the production scale setup. Both in-series and in-parallel in-line scavenging are very often applied in development of such processes For in-series scavenging, primary and secondary cartridges based on different scavenging mechanisms can be applied to improve efficiency. In-parallel scavenging makes cartridge exchange possible without disturbing the process.
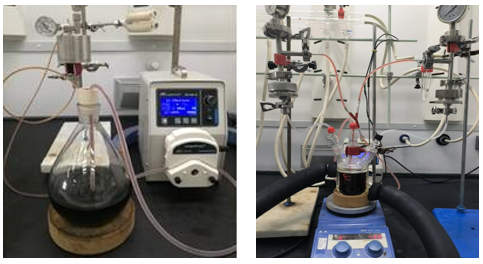
Figure 1 Metal scavenging experiments
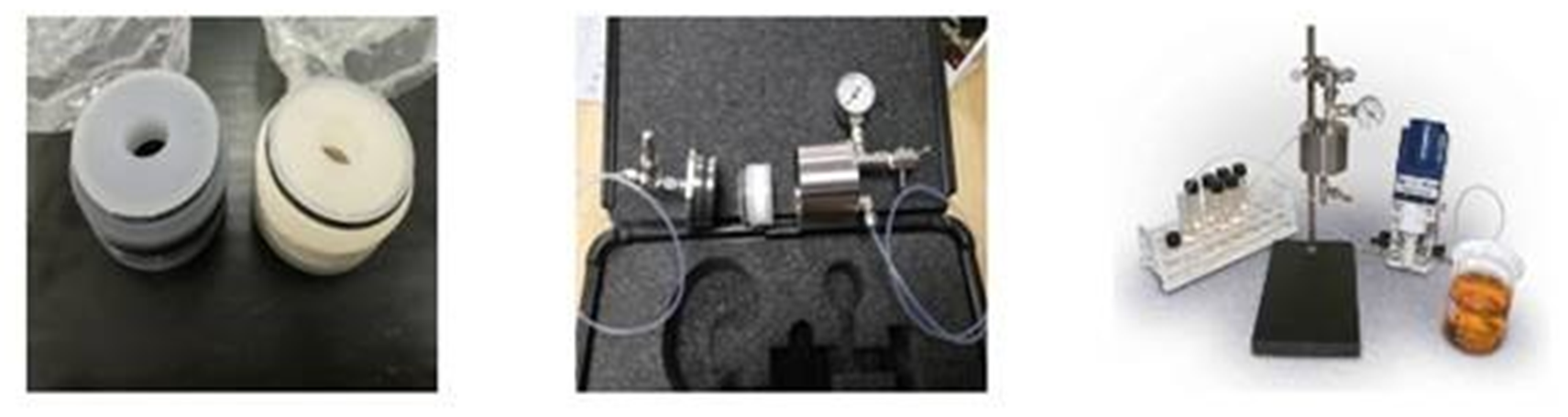
Figure 2 Tools kit for metal scavenge screening
Are there any literature precedent for technical scale in-line metal scavenging with practical in process control?
A pilot scale operation without in-process control has been reported[3]. But large scale metal scavenging with practical in process control has not been reported in literature. In production facilities dedicated to single processes or when extended production runs are performed, specific PAT techniques can be installed (e.g. in-line spectroscopic measurement). However, in a typical CDMO operation where production runs are short and multi-purpose / multi-product equipment is used this option is less practical and simpler, more flexible solutions might be preferred.
What is the capability of large scale metal scavenging and de-colorization in CARBOGEM AMCIS Shanghai plant?
The CARBOGEN AMCIS Shanghai plant has multiple setups of metal scavenging devices up to Ø 0.5 m x 1.5 m with exchangeable cartridges. The scavenging devices can be in-series or in-parallel according to the process need (Figure 3).
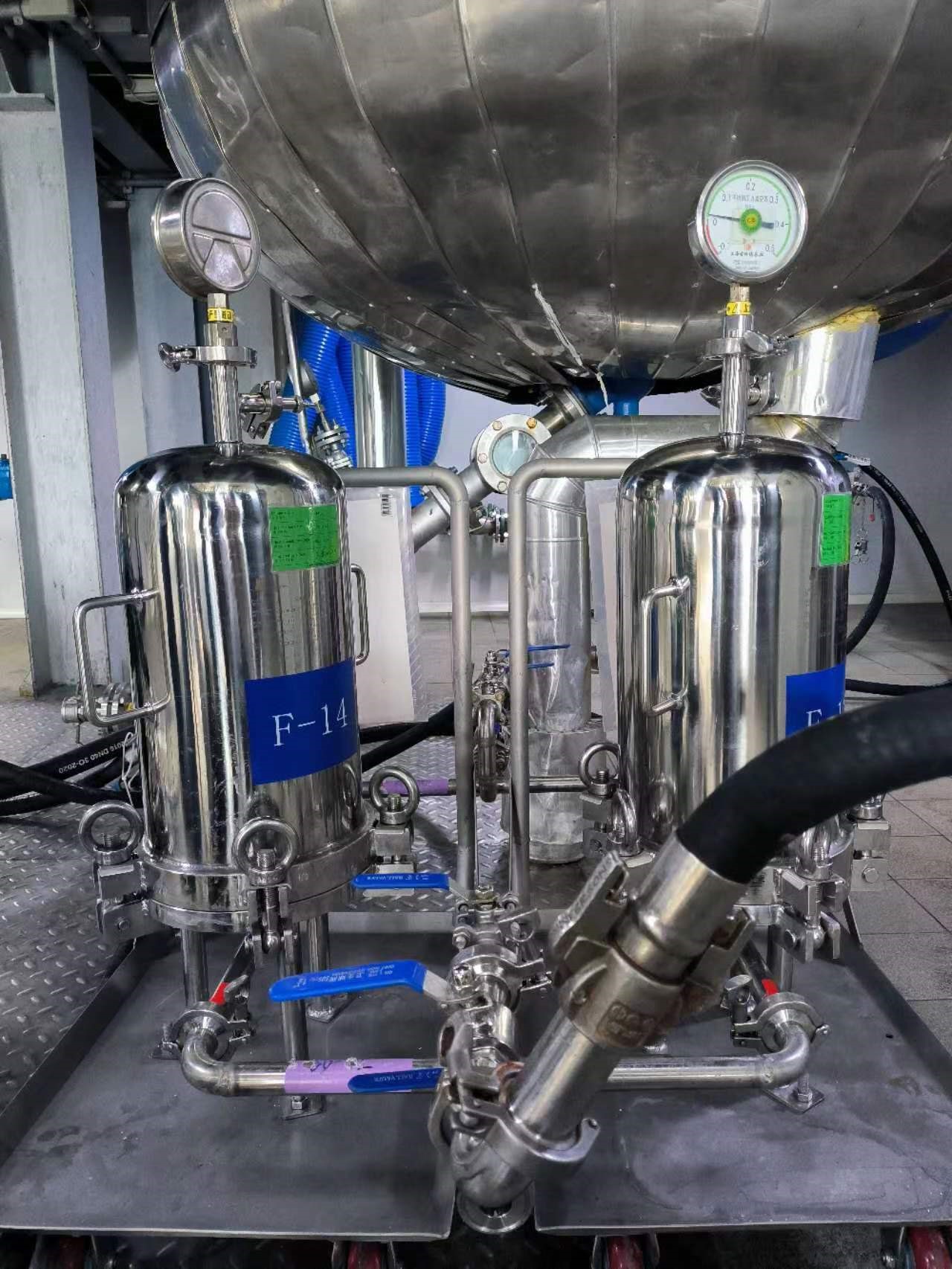
Figure 3 Large Scale Metal Scavenging Device
Practical In-Process Control
While there are semi-quantitative quick tests available in the market such as Quantofix® for copper, zinc and cyanides etc., the requirement for a fast in-process test for palladium content remains unmet.
As color is almost always associated with the level of metal content, in particular for palladium catalyzed cross-coupling reactions, a practical in-process control by colorimetric comparison with Pantone color chart has been established allowing quick IPC and applied in API campaigns.
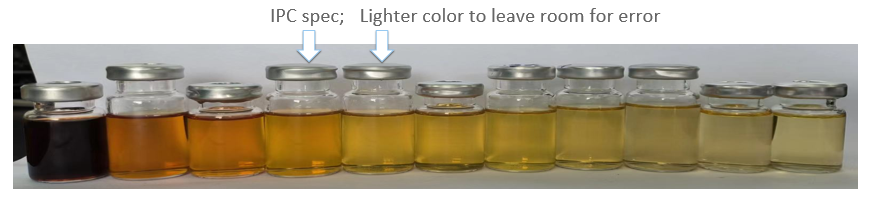
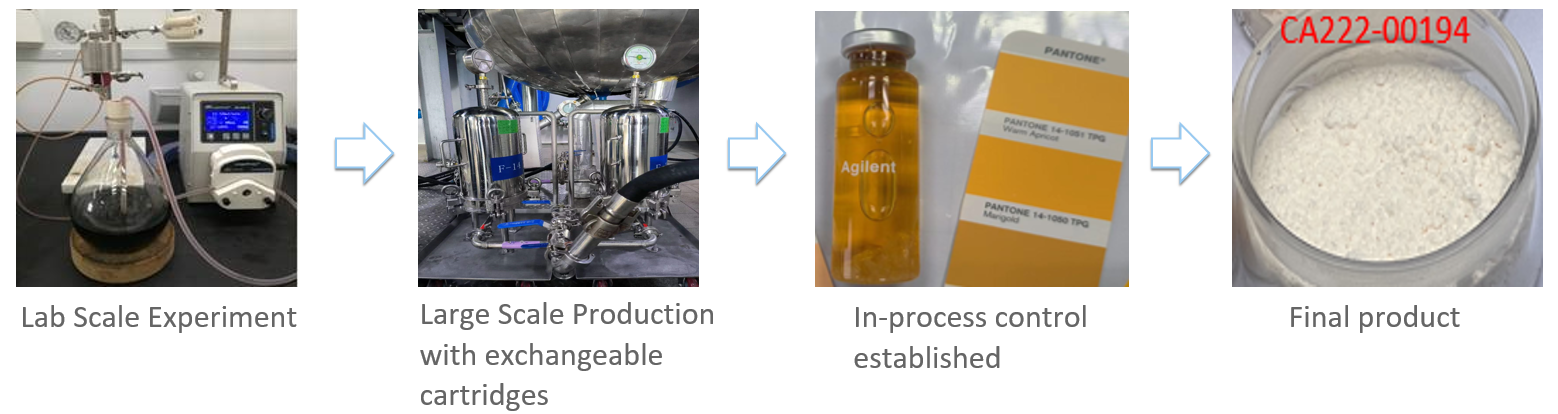
Figure 4 Development of colorimetric IPC method and application
Case Studies
With the robust metal-scavenging and associated decolorising process developed by the SH R&D team, the Shanghai site has successfully accomplished a variety of projects on pilot to large scale.
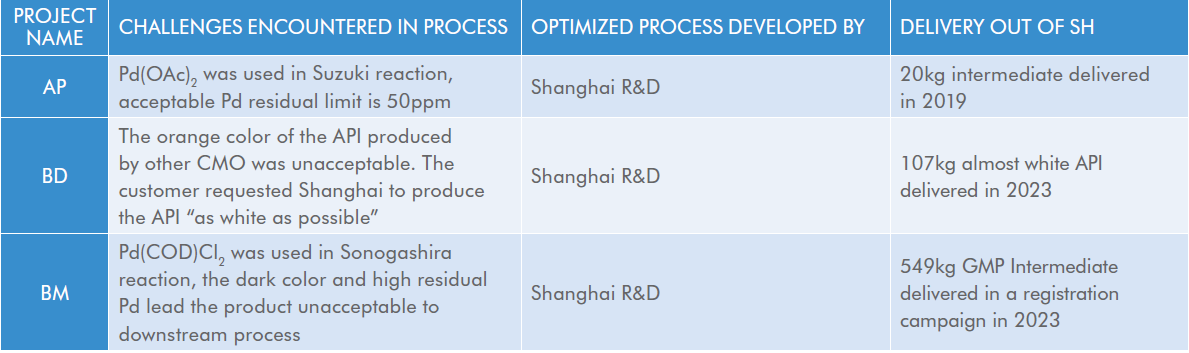
About CARBOGEN AMCIS Shanghai - Large scale manufacturing of raw materials, intermediates and API
Shanghai, the largest economic and trade center in China, contains our fully self-supporting GMP compliant development and production site. Our facility is located in the Shanghai Chemical Industry Park (SCIP) and is designed for large-scale manufacturing of raw materials, intermediates and API.
The site is equipped with 16 reactors, segregated into five separate suites and has reactor capacities from 500 L to 6300 L. With an international team of highly qualified specialists, our facility can provide efficient and scalable solutions to customers globally.
The Shanghai site is part of CARBOGEN AMCIS group, a leading service provider, offering a portfolio of drug-development and commercialization services to the pharmaceutical and biopharmaceutical industry at all stages of drug development. With nine sites around the world (4 in Switzerland, 2 in France, 1 in the UK, 1 in the Netherlands and 1 in China), the integrated services provide innovative chemistry solutions to support timely and safe drug development, allowing customers to make the best use of available resources.
Activities
- Large scale manufacturing of raw materials, intermediates and API
- Capable of manufacturing highly potent chemicals up to category 3
- Analytical capabilities allow GMP product release and analytical support for development activities
Are you looking for an active pharmaceutical ingredient manufacture in China? CARBOGEN AMCIS offers its drug development and manufacturing services in China.
Contact us now if you would like to know more about our pharmaceutical act!
[1] ICH Q3D Guideline or Elemental Impurities
[2] Guideline on the specification limits for residues of metal catalysts CPMP/SWP/QWP/4446/2000
[3] Scaling up Metal Scavenging Operations for Pharmaceutical Pilot Plant Manufactures Gloriana, R., Sadler, R., Wilkes, R.D.; Org. Process Res. Dev. 2011, 15, 6, 1396–1405